In the following article, Malcolm Metcalfe (a SMET member), explores the world of DSG lathes from around the 1970s.
Dean, Smith and Grace: The best medium sized lathes. Probably.
In the aftermath of the second world war, although hard to believe now, the UK was a powerhouse of industrial activity. It had innumerable machine tool manufacturers including Herbert, who at that time was the largest in Europe. However whilst some products were mediocre others were constructed to exacting standards sometimes in rather eccentric circumstances. In this regard no company exceeded the standards of Dean, Smith and Grace (DSG or DS&G), founded in 1865 in the mill town of Keighley, North Yorkshire. To give you some idea of their eccentricities the workforce were given bespoke white starched overalls, hammers were made in house from used railway lines and canteen cutlery was engraved with the company’s initials. Furthermore DSG did not demean itself producing piffling little lathes - they started with 13” center machines which weighed twice as much as a contemporary and equivalent capacity Colchester Triumph. The factory was extremely well equipped having the capacity to produce lathes from 13 to 30 inch swing and up to 256 inches between centers. Each lathe was therefore virtually custom made. Quality control was second to none with in house metalogical, chemical and metrological laboratories.
If you were a customer wanting say a 25 inch swing machine firstly you had to decide on a light, medium or heavy-duty machine. Remembering that a DSG light duty lathe was likely still far more robust that any competitor. The light duty machines were “jacked up” Type 21s with a 24” center height, the medium duty machine was a Type 25 (itself able to be specified as a light duty Type 30) and a heavy-duty machine was a Type 26 which was derived from a Type 30. Then you could specify the bed length, speed range, tool post and optional extras such as chucks. One can only speculate at the cost of these machines especially as confirmatory financial details are few and far between. However a quote was found regarding a University tendering for a well specified Type 17 for £30k + in the mid 1970’s. To put things in context a new Range Rover was £2000 in 1971. A Type 25 was probably nearer £100k. A lot of machines were sold to Rolls Royce or bought on their recommendation. It is testament to their quality that a great number of these machines have survived. Infact the hollow spindle Type 25P still remains the machine of choice in the Oil and Gas Industry for turning and threading pipes.
Unfortunately, in the 1970’s even the mighty DSG was not immune to the financial difficulties of that era with the usual UK-wide slow adaption of modern technology (eg CNC). This of course together with reputed managerial ineptitude also killed Herbert. So in came Monarch from Minnesota USA. They appear to have been relatively cash rich and wished to avail themselves of DSG’s expertise to upgrade their machine portfolio which was looking very old fashioned at this time. Although one cannot be certain after all this time but it looks like DSG had been designing a modern range of lathes with the help of Rolls-Royce which was then bankrolled into production by Monarch. Monarch itself also became bankrupt and now exists as a broker for new machines as well as providing spare parts for their fabulous small 10 EE lathes. DSG survived too and still provides most spare parts for their older machines. They are now based in Halifax. A proud workforce of over 1000 was reduced to 17 at the time of moving.
The fundamental changes made to the “smaller” machines was to reverse the motor position so that it no longer protruded from the base. The ways were altered from a double V to a flatter orientation and the machines were made more angular in keeping with the fashion at that time. The machines were also provided as standard in both metric and imperial executions. Oddly a limited range of the older machines was also continued and the author has seen a Type 25 from the early 1980’s although it might have been a factory rebuild.
It is likely that the first “modern” DSG was the HarDSGlyde1810 from the late 60’s. My advice is DO NOT under any circumstances buy one of these! The machine seems to have been built to replace the Toolroom version of the Type 17 (Type 17T) and had a lot of innovative technology such as an immensely hard bed (hence the corny name) and a sophisticated and unique Matrix clutch which allowed access to a large range of speeds without stopping the machine. Matrix is still in business in Brechin but apparently does not have any drawings, literature or parts for these clutches…
Anyway in the 70’s the main range of lathes seems to have been as follows:
- New 1307 (14” swing and 7” swing across the topslide). Usually 40” between centers but 30 and 50” were available. Width across bed shears = 13.375”. Spindle bore = 2.0625”. Four speed ranges (12 F & R) but most common 29-1600 rpm via belt overdrive. Optional Gap with 22” swing. Best seller.
- New 1609 (17” swing and 9” across topslide), 40-60" between centers. Optional Gap. Very common as relatively good value for money and optimal size for toolroom or maintenance shop. Probably too big for a model engineering lathe.
- New 1709 (17” swing and 9” across topslide). Although seems the same as the 1609 this is a much more robust and sophisticated machine. Considerable accessories available. Gap bed optional and bed lengths up to 120”.
- New 1910 (19 inch swing and 10 inches across the topslide).
- New 1910T (toolroom variant of above). Many sold to the Forces as had ability to undertake relieving and hence ability to make milling cutters. No gap version as is usual practice for a rigid toolroom machine. 2 speed motor with 32 F & R speeds. Very well specified and very expensive. Bore 3.2”. 17.5” across bed.
- New 2112.
- New 2415.
- The 1709, 1910, 2112 and 2415 all shared the same bed and the entire range nearly satisfied the rule of thumb that a toolroom lathe bed width should equal its swing.
- Surfacing and Boring variants of 1609, Type 21 and Type 25 (+30 XS special)
- Type 18 and 21
- Type 22 and 25
- Type 26 and 30
- Type 36Light duty (LD) or extra size (XS) (jacked up type 30)
- Type 25P and 30P for tubulars in O & G industry.
- One large CNC machine.
I remember about 20 years ago, before being taken over by Newsmith Stainless, DSG were advertising a range of large CNC machines together with rebuilding existing machines or extending their bed length by using (presumably) an old stock of bed castings. The original CE of the company then seems to have taken over again and had an idea of producing very large milling machines. Only one was completed then the company was sold with a concentration on rebuilding older machines and selling spares. It was taken over by the Machine Tool Technology Group (MTTG) and now concentrates on machine tool repairs, servicing, automation and spares with new products apparently being developed.
I wish them luck for the future.
Tony Griffiths of the popular “lathes” website has more details on the history and products of this illustrious company which is well worth reading.
So is there any relevance of these machines for the model engineer? My answer to this is a resounding “yes” as the owner of a 1307 x 40 (actually a 1307 x 48?!). It’s exactly as our colleague (Northern Steam) describes. All controls are set out just as one would wish, the accuracy is outstanding, the ability to move metal is in a different league to the usual model engineering lathes. It swops from imperial to metric (and vice-versa) at the flick of 2 levers. There are also plenty about although I would not suggest anything bigger than a 1307. Even this “baby” is 2.5 t and is top-heavy so be careful! Also worth pointing out is that some accessories such as steadies are difficult to obtain or expensive (eg chucks). You need a 1600 or 2240 top speed especially as the belt overdrive removes the risk of gear marks from the finishing cuts. This is of course being easy to measure with a Talyrond that I am sure you have all put away for a rainy day…
Most will have had a relatively hard life but there are still some lovely machines about. Careful inspection will pay dividends although a good alternative is to buy one from a reputable dealer. Mine came from an auction at Black and Decker in Gateshead and was geometrically refurbished and painted by Blue Diamond Machine Tools in Shildon whom I regard as the foremost DSG experts. However, this work was not cheap and never will be but the end result is fantastic. If you want a bigger lathe to complement your workshop one of these in my humble opinion is infinitesimally better than a worn-out Colchester or Harrison.
Herewith a short picture essay to show the machine doing different jobs. However on the Brookes machine tool website is a picture of my lathe just freshly painted. I don’t know how it got there and don’t care but this is another company with a good reputation.
Illustration 1
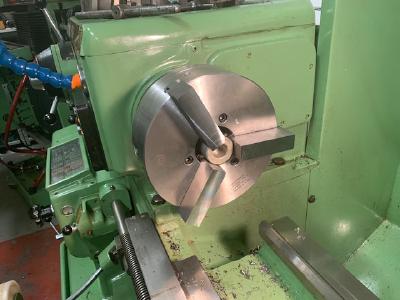
Use of 3 jaw chuck with soft jaws in use. There is a blank of the correct finish dimension within the chuck so that the chuck will accurately grip the workpiece to the tolerance of the machine. In this case <0.001 inch.
Illustration 2
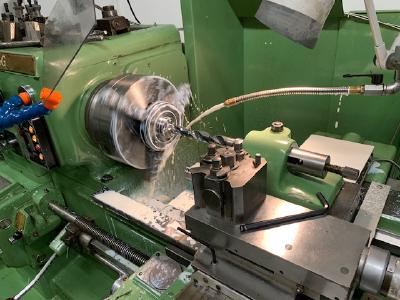
Machining in progress using the drilling attachment (drill bracket in DSG speak) to hold a MT drill. Coolant used as this is EN19T with a HSS drill.
Illustration 3
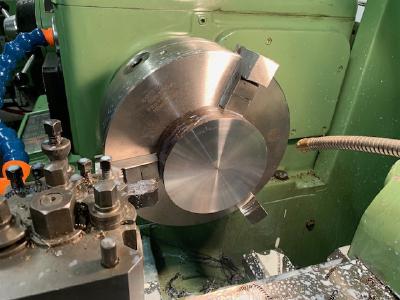
Larger diameter billet of tough EN 24T carbon steel. Surface finish is excellent at 220 rpm, 20 thou feed. Carbide tipped tool with no coolant. Chips are blue/yellow.
Illustration 4
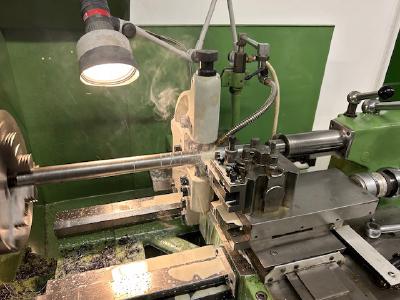
Travelling steady in use on long job (c 30 inches). When external diameters finished end of bar will be screwcut at 5/8” x 11tpi using fixed steady for support. Good finish in EN8 although not my favorite steel.
Illustration 5
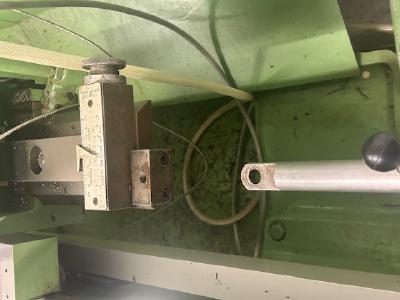
Taper-turning attachment. Not often used but when required nothing will beat it – except CNC…
Illustration 6
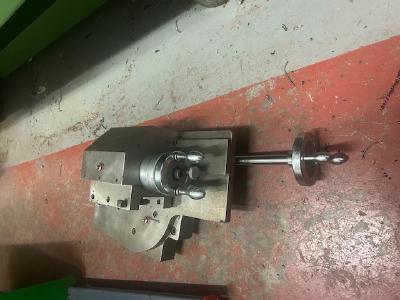
Ball turning attachment. Very few of these sold and now obsolete due to CNC.